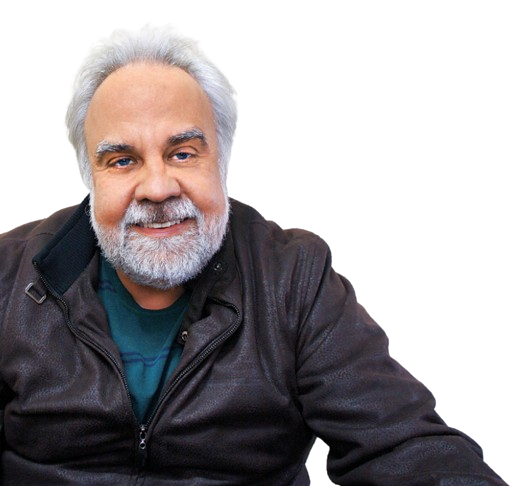
Engenheiro civil Carlos Alberto Freire de Andrade
Lopes, ou apenas Carlos Freire, como é conhecido, é uma autoridade quando o assunto é estrutura metálica. Formado em 1980 pela Escola de Engenharia Mauá e diretor técnico do escritório que carrega o seu nome, possui mais de três décadas de experiência no segmento. No decorrer da carreira desenvolveu know how em nichos específicos da construção em aço, como projetos de helipontos, edifícios para empresas petroquímicas, além de atuar
no desenvolvimento de projetos de recuperação estrutural.
Porém, mais do que isso, se tornou um especialista em CNC (sigla para controle numérico por computador). Trata-se de um sistema de fabricação de estruturas metálicas a partir de arquivos enviados por um software de modelagem 3D, que contém todas as informações relacionadas à estrutura. Utilizada há mais de 20 anos em países europeus e também nos Estados Unidos e no Japão, a tecnologia ainda é recente no Brasil, e, segundo o engenheiro, pode impulsionar ainda mais o uso de sistemas construtivos industrializados no mercado brasileiro, ainda definido por soluções artesanais. Freire, associado da ABCEM desde
2002, durante a entrevista para a Revista Construção
Metálica, falou sobre sua experiência com o CNC e as vantagens deste processo
em relação aos métodos convencionais.
Confira a seguir:
Desde quando o seu escritório utiliza o CNC nos projetos?
Carlos Freire – Começamos a utilizar em 2002. Em alguns países europeus, nos Estados Unidos e no Japão o processo de fabricação automatizada de estruturas metálicas por CNC é empregado desde a década de 1990. Conheci o processo ao visitar empresas na Europa.
Na ocasião, adquiri um software finlandês de modelagem 3D com resultados de arquivos para operação em CNC.
Qual foi o primeiro projeto que você utilizou esse tipo de tecnologia?
Freire – A primeira obra foi o heliponto do Hospital Paulistano, em São Paulo,
em 2003. Ele é todo em estrutura metálica, parafusado e totalmente projetado e produzido com o uso de CNC.
Como foi utilizar um sistema ainda novo no país?
Freire – Em 2002 tínhamos muita dificuldade em manipular o programa de modelagem porque não existia outro usuário no Brasil. Na época, delegamos a um único profissional do escritório a missão de utilizar o software. À medida que surgiam dúvidas, recorríamos ao fabricante na Europa.
O problema é que a empresa conhecia o software, mas não o sistema construtivo em aço. Hoje, com a disseminação da tecnologia é mais fácil a troca de ideias. Sem contar que o treinamento e a aprendizagem tornaram-se mais fáceis à medida que outros profissionais se especializaram.
Pode-se dizer então que a tecnologia foi incorporada pela maioria dos escritórios brasileiros?
Freire – Aos poucos, o sistema está sendo disseminado aqui no Brasil. Temos, de fato, pleno conhecimento da tecnologia, embora exista uma quantidade pequena de profissionais que trabalhem com ela. Porém, trata-se de pessoas muito qualificadas e realmente aptas a fazer o que se faz globalmente.
Como o CNC pode ser definido dentro do processo de fabricação da estrutura metálica?
Freire – O CNC é uma parte do processo de produção da estrutura metálica. Existem algumas etapas anteriores, como o cálculo e o planejamento da estrutura.
Nesta última, a obra é detalhada peça a peça, por meio de um software de modelagem com posição das perfurações, bem como das medidas exatas das peças.
Nessa etapa são geradas as informações necessárias para que a máquina de CNC trabalhe. Logo, a operação em CNC pode ser feita de duas maneiras. Desenha-se a peça que se quer produzir e uma máquina é programada para executar o que está no desenho. Mas já tivemos avanços. Atualmente, o próprio programa é utilizado para realizar o detalhamento da estrutura, criando um arquivo no formato do processamento usado nos equipamentos CNC. Esse arquivo vai diretamente para a máquina que executa o serviço.
Quais são as vantagens em relação ao sistema convencional?
Freire – Quando se emprega alta tecnologia, muitos valores passam a ser agregados. Uma vantagem está diretamente relacionada ao custo. Uma estrutura projetada e fabricada por CNC chega a custar 20% a menos do que a produzida de forma convencional, uma vez que as chances de erros são praticamente nulas. O software possibilita o dimensionamento exato de cada peça e também de todas as ligações. Todo o detalhamento é enviado para o computador, que realiza o trabalho em um sistema fechado em 3D. Outra vantagem é que ainda é possível dar nome às peças, facilitando a montagem, então realizada de maneira sequenciada em função das identificações feitas. O mais interessante é que o sistema permite a criação de uma maquete eletrônica da obra. Quando os arquivos das peças que compõem essa maquete eletrônica são gerados, a máquina corta e perfura exatamente conforme o modelo determinado pelo sistema. Além de qualidade, o processo imprime velocidade na execução do projeto.
Aos poucos, o sistema está sendo disseminado aqui no Brasil. Temos, de fato, pleno conhecimento da tecnologia, embora exista uma quantidade pequena de profissionais que trabalhem com ela.
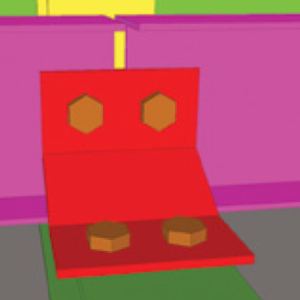
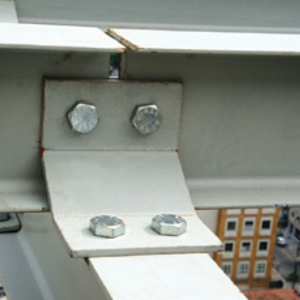
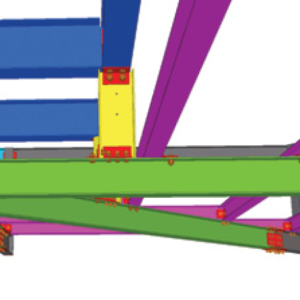
Como é a oferta de softwares atualmente?
Freire – Hoje o mercado dispõe de cinco ou seis softwares de modelagem 3D de fabricantes de origens diferentes.
Cada programa desses tem um preço e uma determinada eficiência, mas todos conseguem trabalhar com o cálculo, o detalhamento e a geração dos arquivos em CNC. Existem diferenças entre eles, porém, são todos muito eficientes.
Com quantos deles você trabalha no escritório?
Freire – Atualmente temos três softwares de modelagem aqui no escritório. Apesar de diferentes, todos geram arquivos de CNC. Normalmente usamos o programa que o cliente tem. Ao realizar uma obra, instalamos o software no computador e carregamos a estrutura que será montada.
Como se trata de um programa inteligente, basta abrir o modelo 3D e clicar sobre uma determinada peça que ele automaticamente mostra o nome do componente e onde ele deve ser instalado.
Existem diferenças de qualidade entre os softwares?
Freire – A diferença entre um programa e outro é que alguns possuem recursos a mais. O que possibilita que alguns desenhos sejam feitos com maior facilidade e velocidade, utilizando recursos que talvez outros não tenham, principalmente em relação ao detalhamento das ligações das peças. Porém, em obras mais convencionais, como edifícios corporativos com estruturas inteiramente em aço, por exemplo, o mais simples consegue atender.
Alguma tipologia de obra exige mais recursos desses programas?
Freire – No setor petroquímico, por exemplo, que denominamos de edifícios de processos. Além da estrutura metálica, é preciso considerar o tipo de tubulação que transporta os elementos químicos no prédio e os vários equipamentos necessários, de maneira que tais informações acabam por interferir no projeto. Neste caso, a base ou piso das estruturas metálicas tem de receber perfurações exatas
para a fixação em pontos pré-determinados.
Eu diria que nesse tipo de obra só é possível se obter qualidade por meio de processos com modelagem 3D, uma vez que todas as informações serão inseridas no CNC. Aliás, ao longo destes 30 anos de experiência com estruturas metálicas, encontrei muitos problemas na fabricação e montagem desse tipo de edifício.
Em geral, isso acontece com construções mais complexas, quando o partido arquitetônico é repleto de curvas. Na Europa, existe uma tendência de projetos executados com estrutura em aço, com essa característica de arquitetura mais fluida e repleta de traços orgânicos. Em construções olímpicas temos muitos projetos assim. Nessa tipologia, as peças são bem
complicadas de se executar, exigindo mais recursos do programa. Os estádios vistos nos Jogos Olímpicos de 2008, na China, são um exemplo.
Qual o projeto mais significativo que você já executou com o uso do CNC?
Freire – Foi uma fábrica inteira do Grupo Ultra no polo petroquímico de Camaçari (BA). São vários edifícios de processos, todos produzidos em 3D e processados em CNC.
O que o sistema em CNC representa hoje para a construção em aço?
Freire – Eu acho fundamental associar não só o CNC, mas toda a modelagem 3D à construção metálica. A tecnologia garante qualidade, precisão, flexibilidade nas formas, além de significativa redução de custos ao projeto como um todo. Costumo dizer que o método descaracteriza o conceito de fábrica de estrutura metálica, criando o de centro de processamento em aço.
Qual a diferença básica entre os dois?
Freire – Em alguns países, particularmente nos Estados Unidos, existem várias empresas que se auto-intitulam steel center, que significa centro de processamento em aço. Isso é muito comum no mercado americano. As construtoras podem escolher entre quatro ou cinco steel centers para fabricar as vigas e entregar direto na obra. Ocorre até de várias trabalharem em um mesmo projeto. Nós tivemos alguns modelos assim no Brasil, mas sem sucesso. Isso mudaria o conceito de fabricante de estrutura em aço no país. Lá quem faz a obra é a construtora, e não quem produz a estrutura metálica. Aqui, muitas vezes, os fabricantes são responsáveis até pelo projeto. Acho que eles ficariam até felizes se funcionassem como um steel center. O fabricante não tem que ter responsabilidades de engenharia, pois isso recai sobre os projetistas. Ele tem que recortar e perfurar o aço, o que representaria um grande negócio para os produtores de estrutura.
Existe algum tipo de restrição para o uso do CNC na fabricação de estruturas metálicas? Ou seja, alguma tipologia de obra o qual ele não seja indicado?
Freire – O CNC funciona bem para a produção de vigas do tipo I, H e cantoneira.
Em uma estrutura treliçada, por exemplo, ele não se aplica tão bem. A menos que se utilize uma máquina para fabricação de treliça em CNC, o que é pouco comum no Brasil. Outra questão importante é que essa tecnologia é mais indicada à construção da estrutura metálica com parafusos.
O que não significa que não exista solda no CNC, até pode ser utilizada num sistema automático, mas a resposta nem sempre é eficiente. Os projetos mais recentes que temos executado lembram as estruturas de rebite, comuns às peças fabricadas durante a revolução industrial inglesa,
completamente sem soldas. Trata-se de obras com montagem 100% parafusadas, com galvanização a fogo. Isso é possível graças ao CNC, que possibilita um corte preciso. A ideia é eliminar o trabalho artesanal, isto é, produzir cada vez mais a estrutura no computador e sem grandes
interferências do homem.
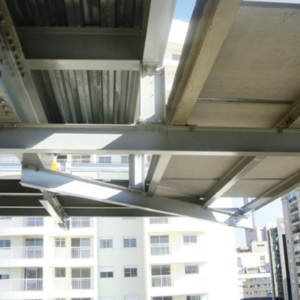
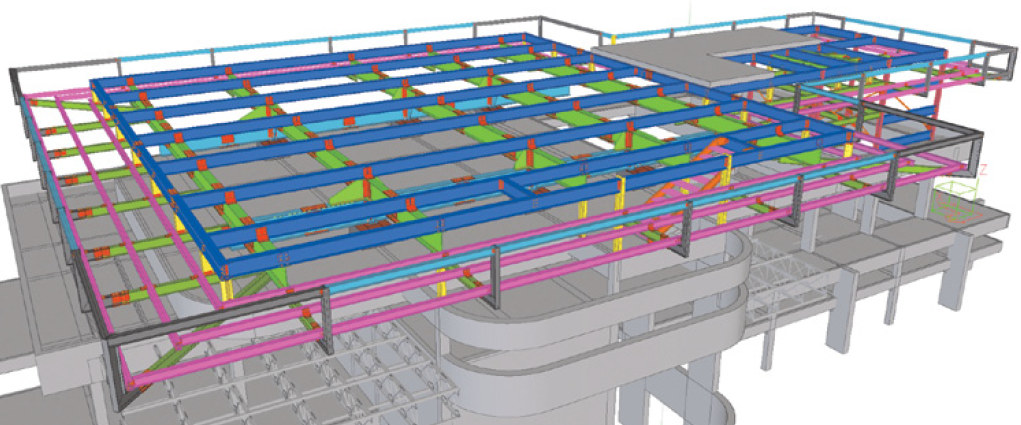
Publicação Especializada da Associação Brasileira da Construção Metálica – ABCEM
Edição 111 | 2013 | ISSN 1414-6517